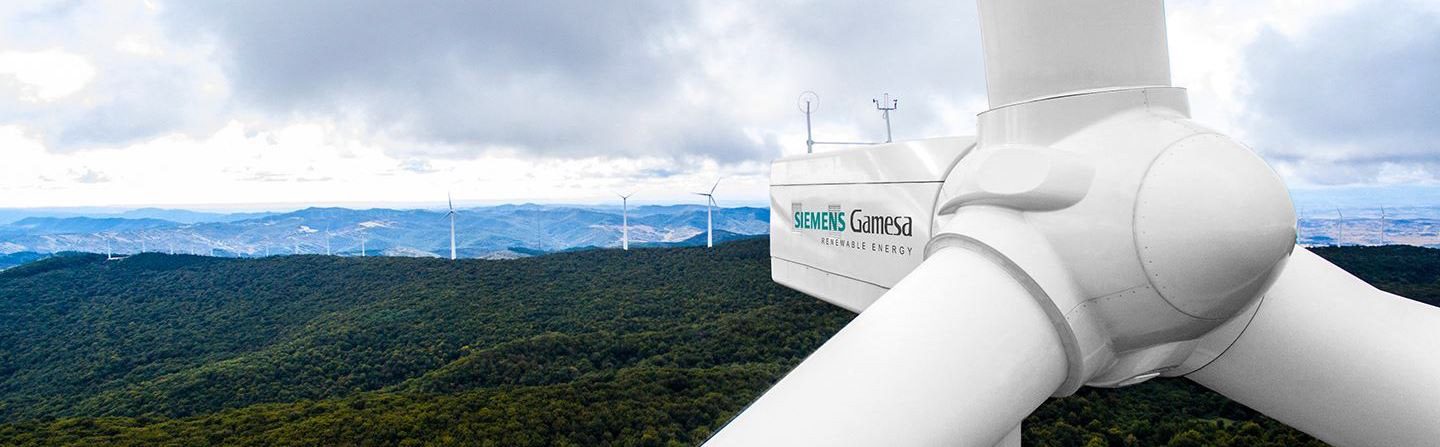
Goal
Improve the Final Inspection process at the Siemens Gamesa Wind Power production facility in Denmark with the help of DAQRI's Augmented Reality Smart Helmet.
Tools

Pain Points
Inspectors have Work Instructions that explain each inspections point but the inspection sequence is decided by each inspector individually. As a result inspection quality varies across inspections and during inspectors can not continue where the last inspector left of following a shift change. Inspectors have to go back to the PC and record in an excel file the issues found including their location based on a 2d grid map. Reports are filled out after performing an inspection from memory making it challenging and time consuming to recall all the right details and updates. During re-inspections inspectors find it difficoult to find previously reported snags to confirm whether they have been resolved.
Planned Features
• AR orientational Guidance from one inspection point to the next
• Context aware inspection points that the inspector can pass or fail
• Virtual snags to mark issues in the physical world
• Hand held camera that streams to the visor to inspect otherwise inaccessible details
Risks
• The inspectors are highly experienced and the concept of being guided by the Smart Helmet was met with scepticism
• The Smart Helmet is heavy and uncomfortable when warn for a long duration
• Text input and selections out of large datasets can be tricky for unexperienced users
• The technicians need to use their hands during the inspection meaning that the UX of the inspection app needs to be fully hands free
Key Stakeholders
I mapped the key stakeholders, to better understand their pain points and possible value gains more clearly. While in the beginning most of our insights and requirements came from innovation team it became clear that we needed to engage with the inspectors as the end user directly to ensure the success of the software.
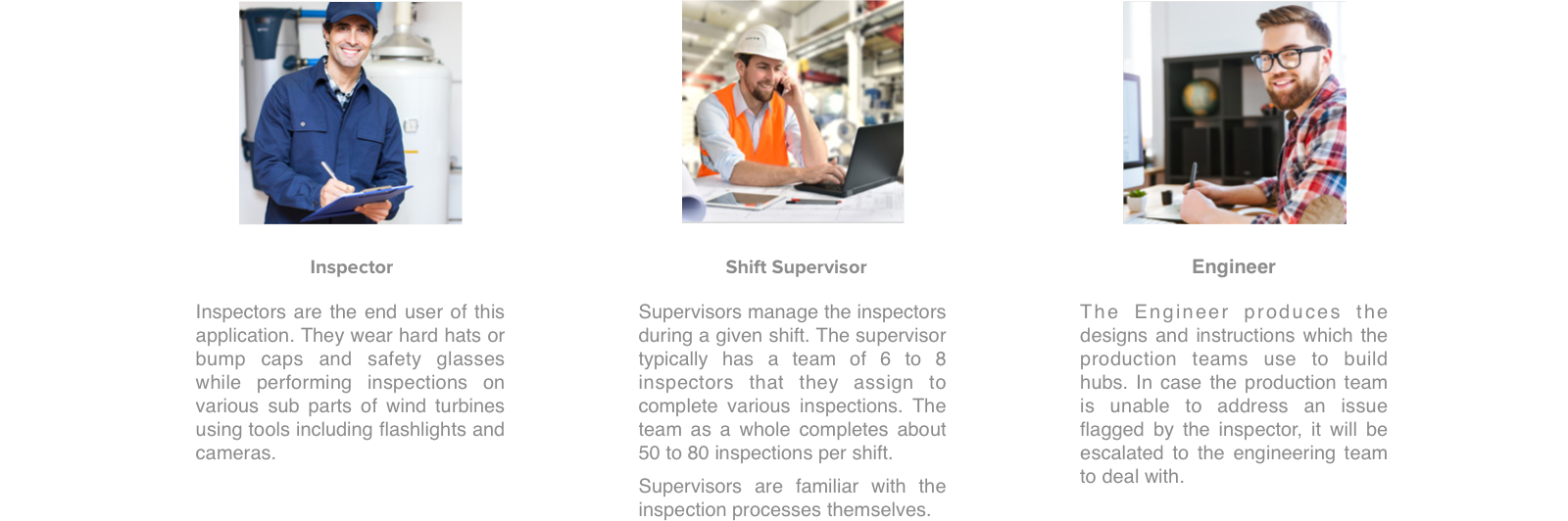
Interviewed and Shadowed the End User
Right from the get go, I involved the in Inspectors who where the endusers of the inspection application in the ideation process. I visited the facility and observed an inspector completing a full hub inspection. Following this onsite we translated the findings into a storyboard and shared it with all stakeholders. Through this I was able to tailor the application to the needs of the inspectors and include app controls that ensured that the inspector remains in the driving seat of the inspection process while benefiting from the technology.
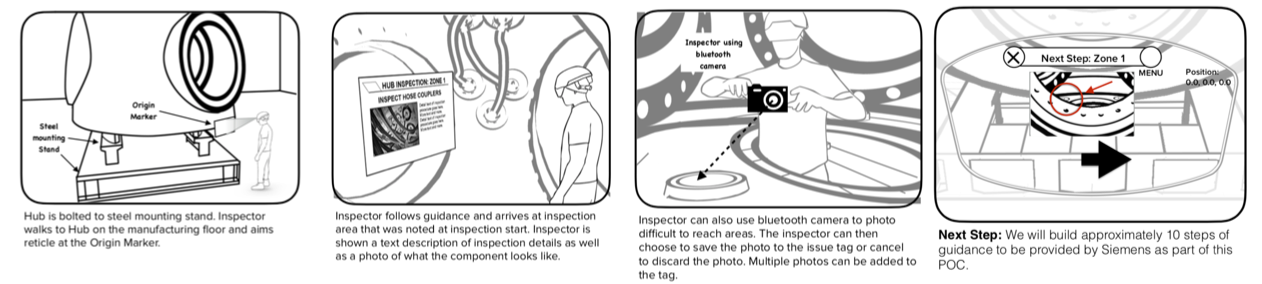
UX/UI Design
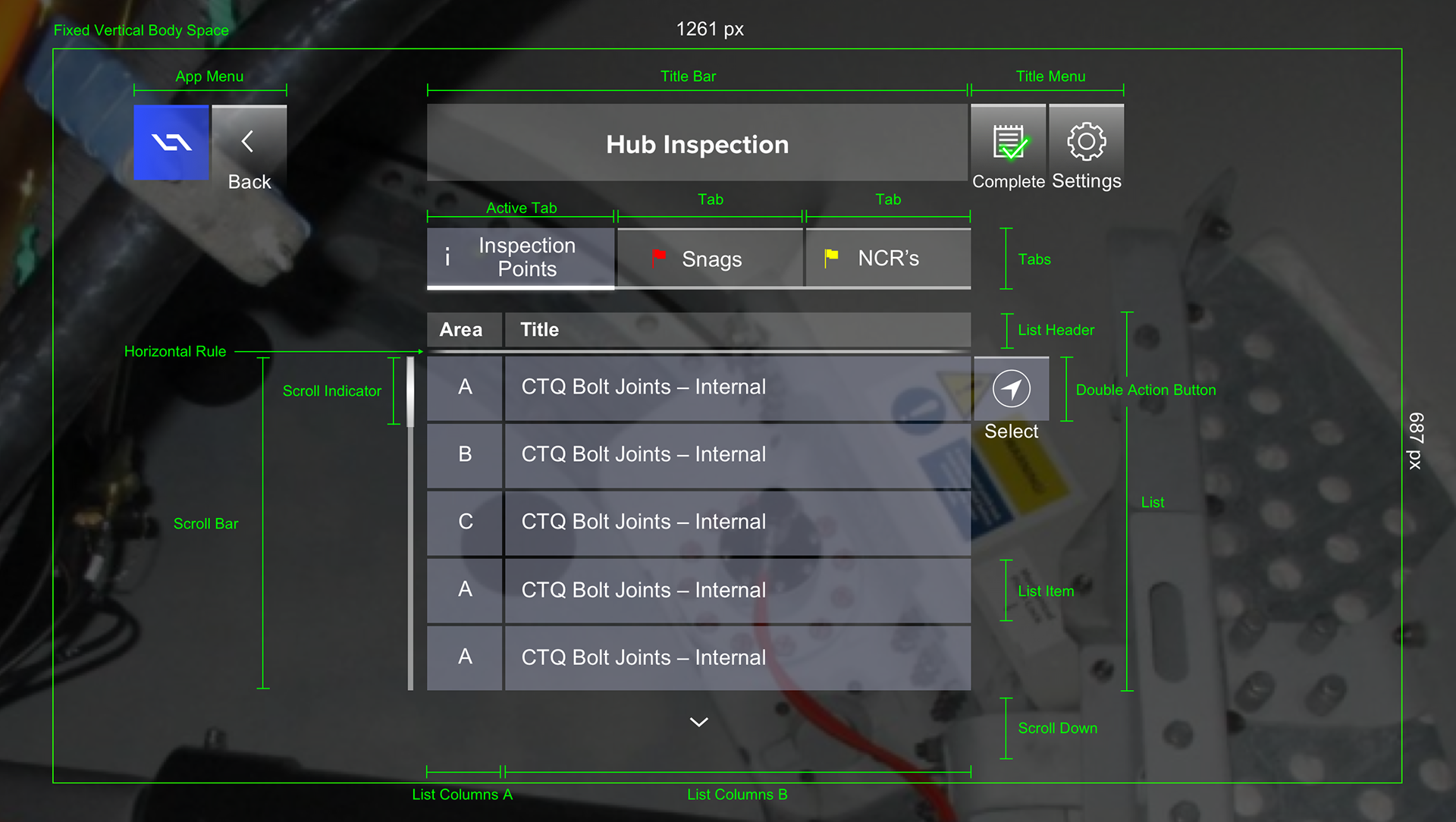
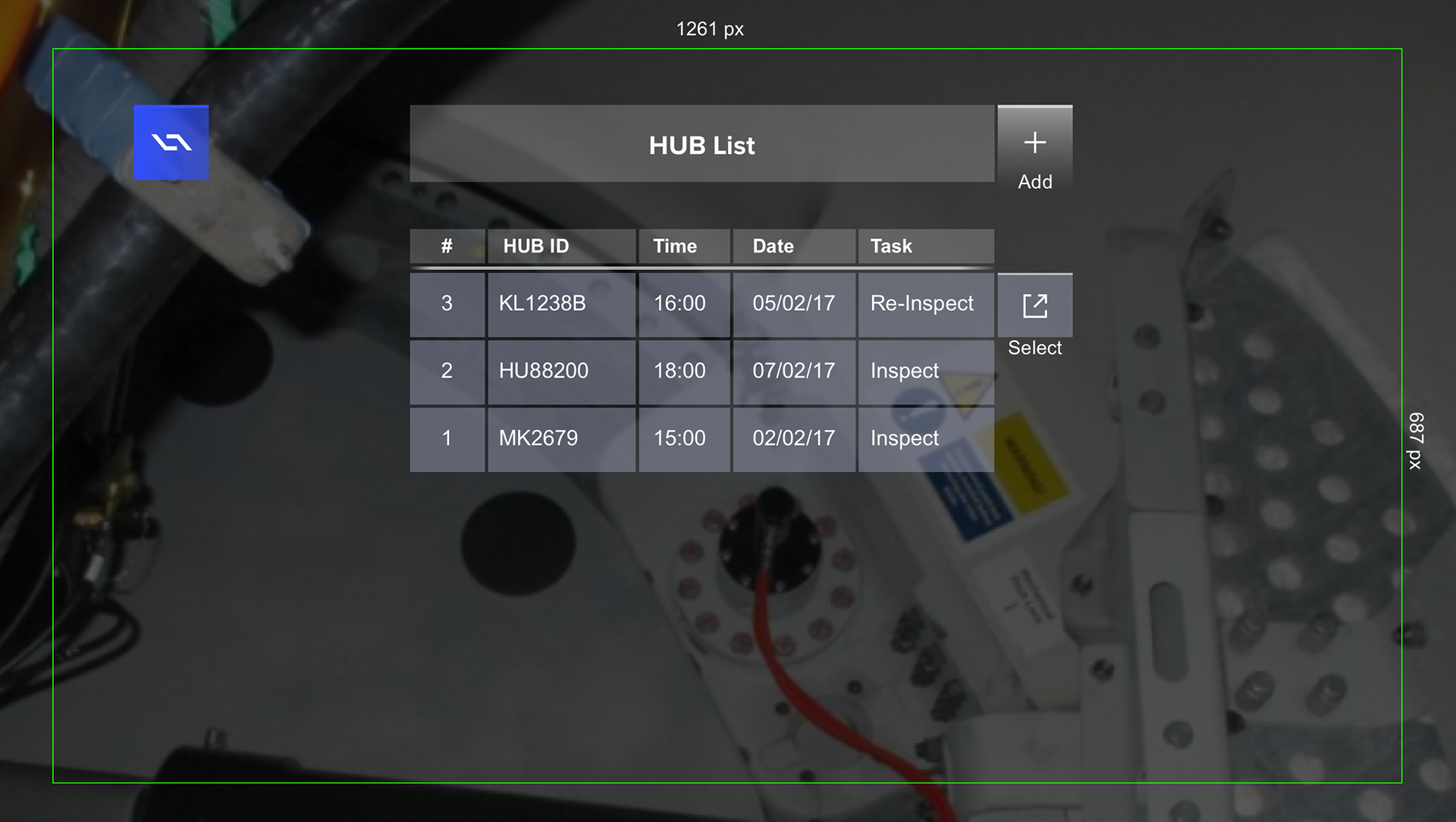
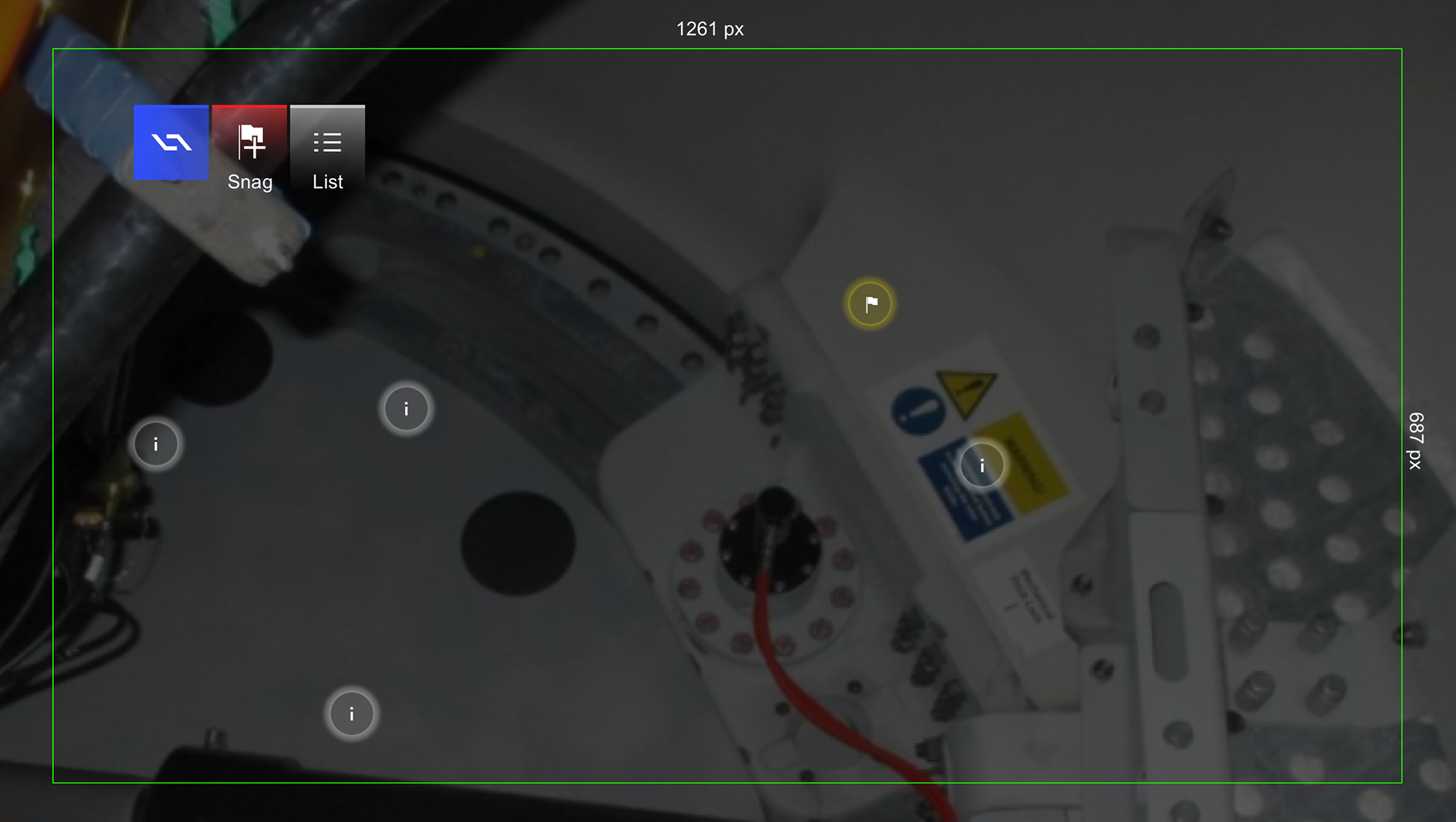
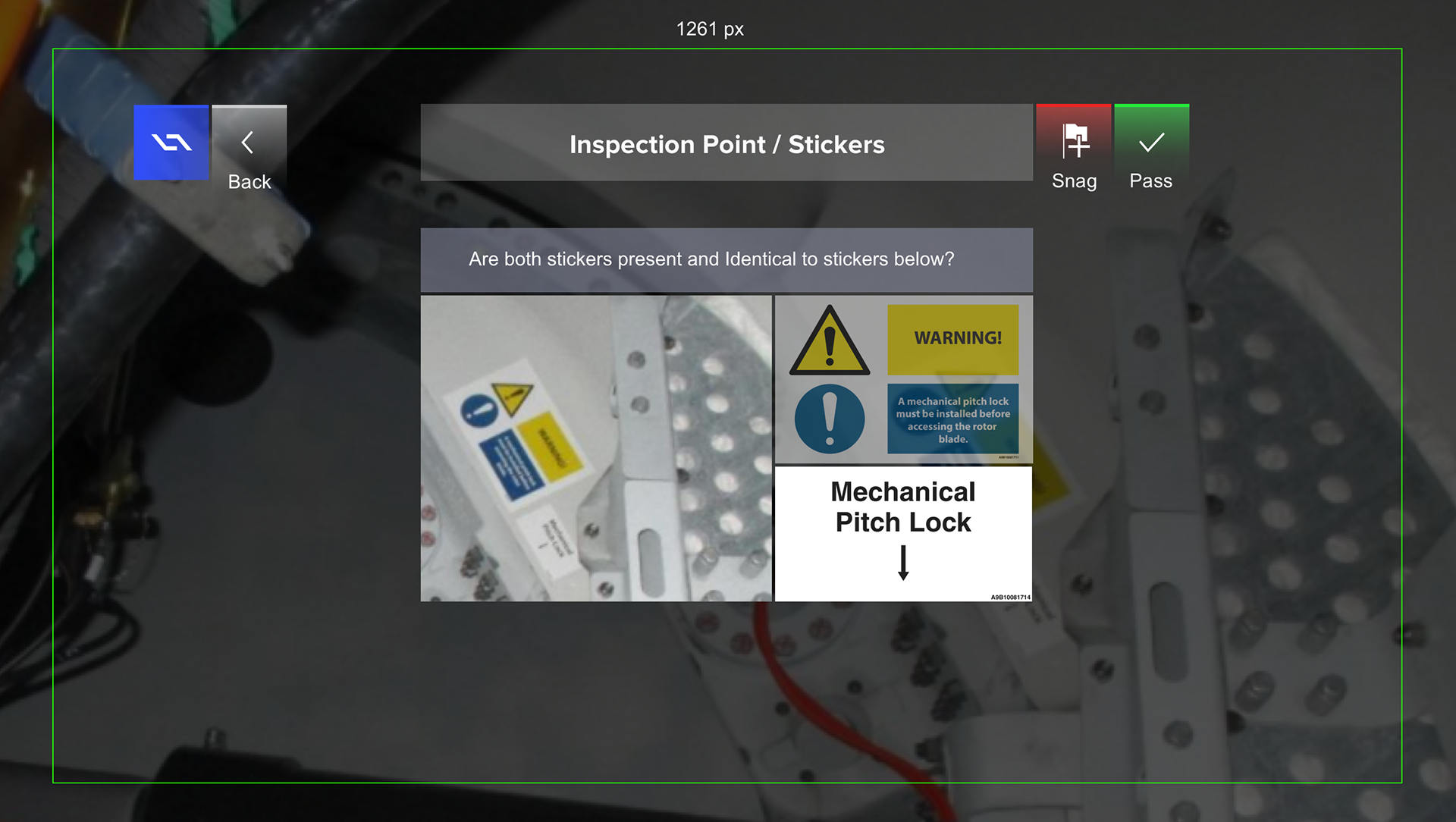
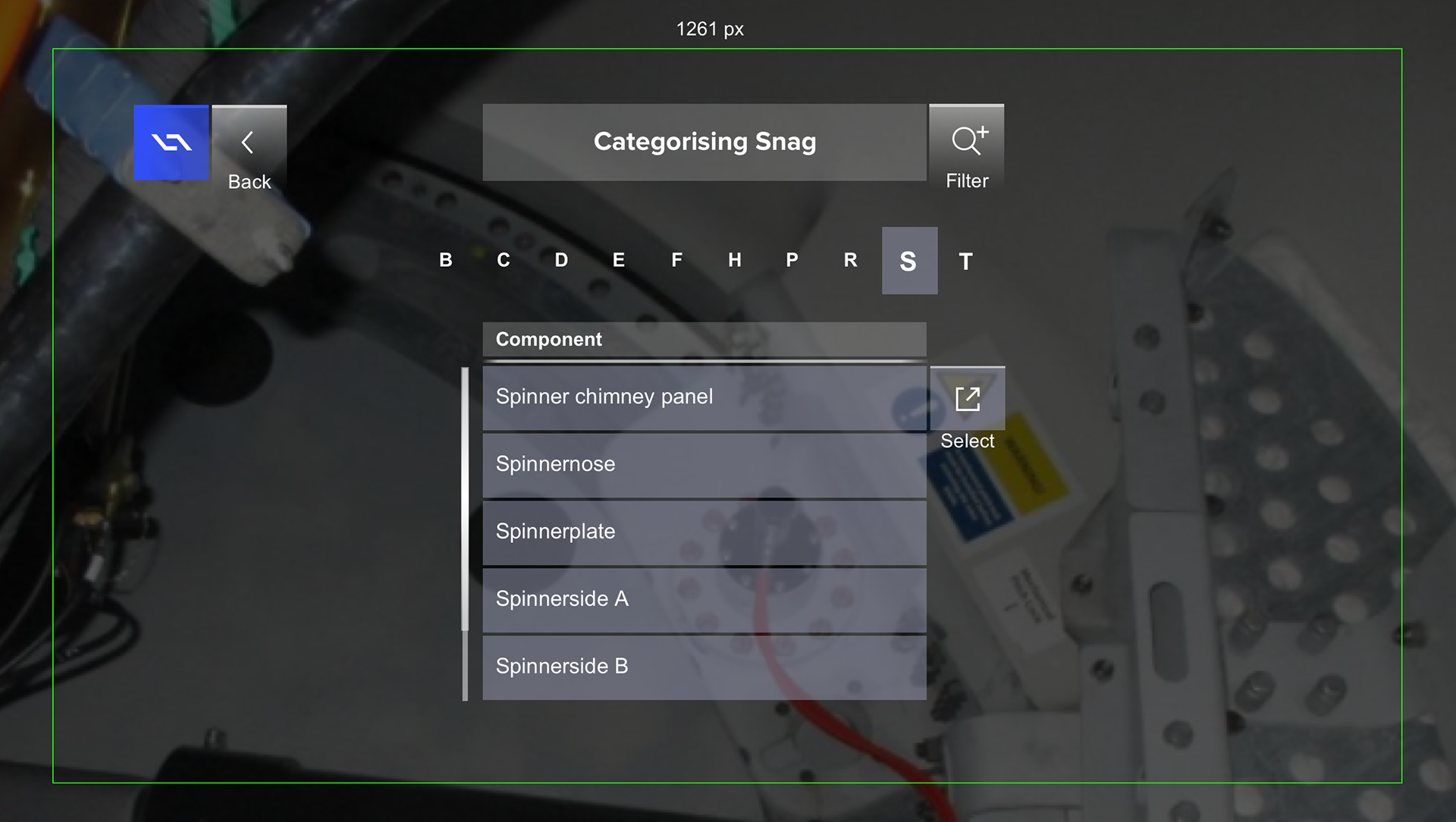
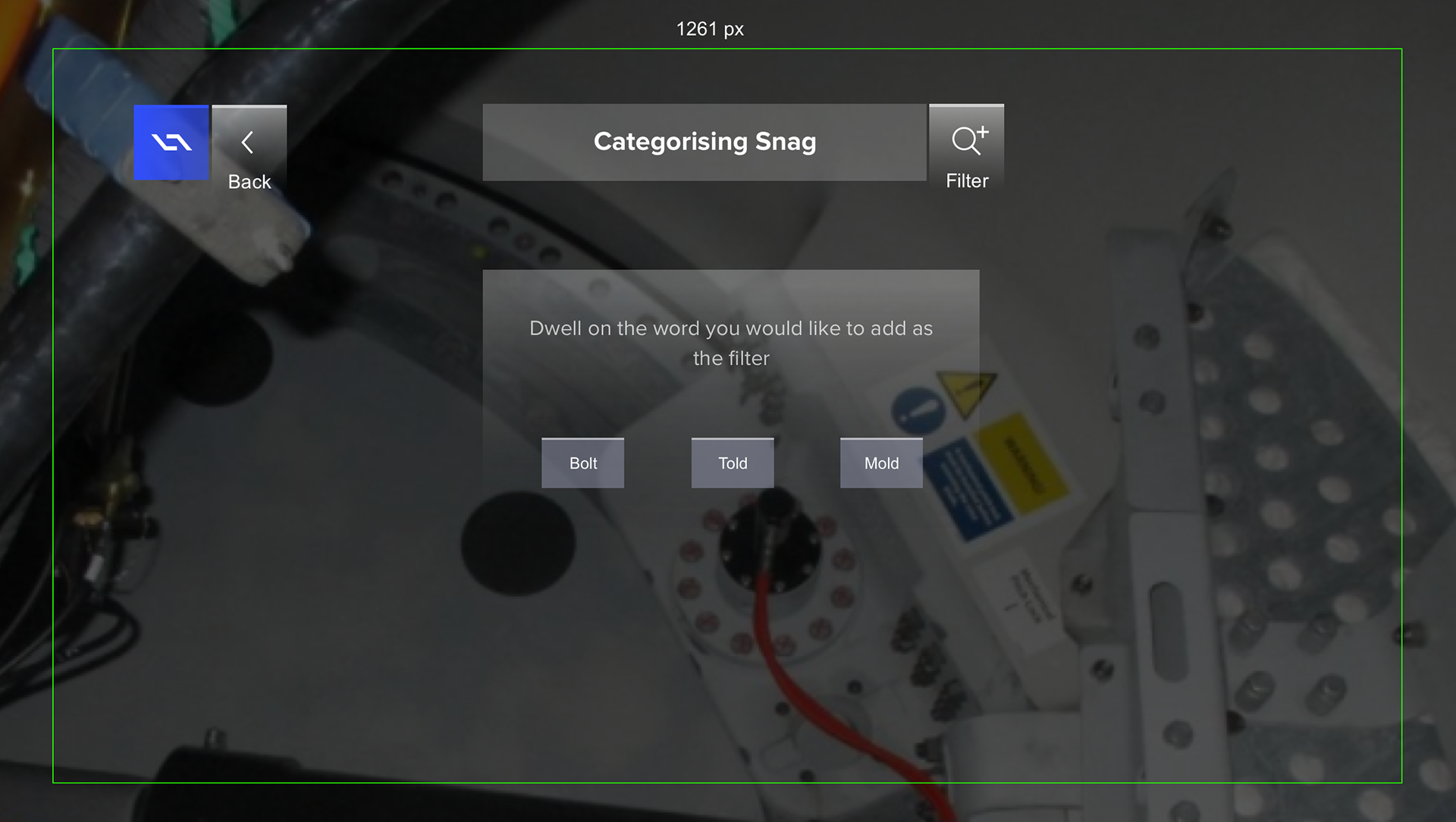
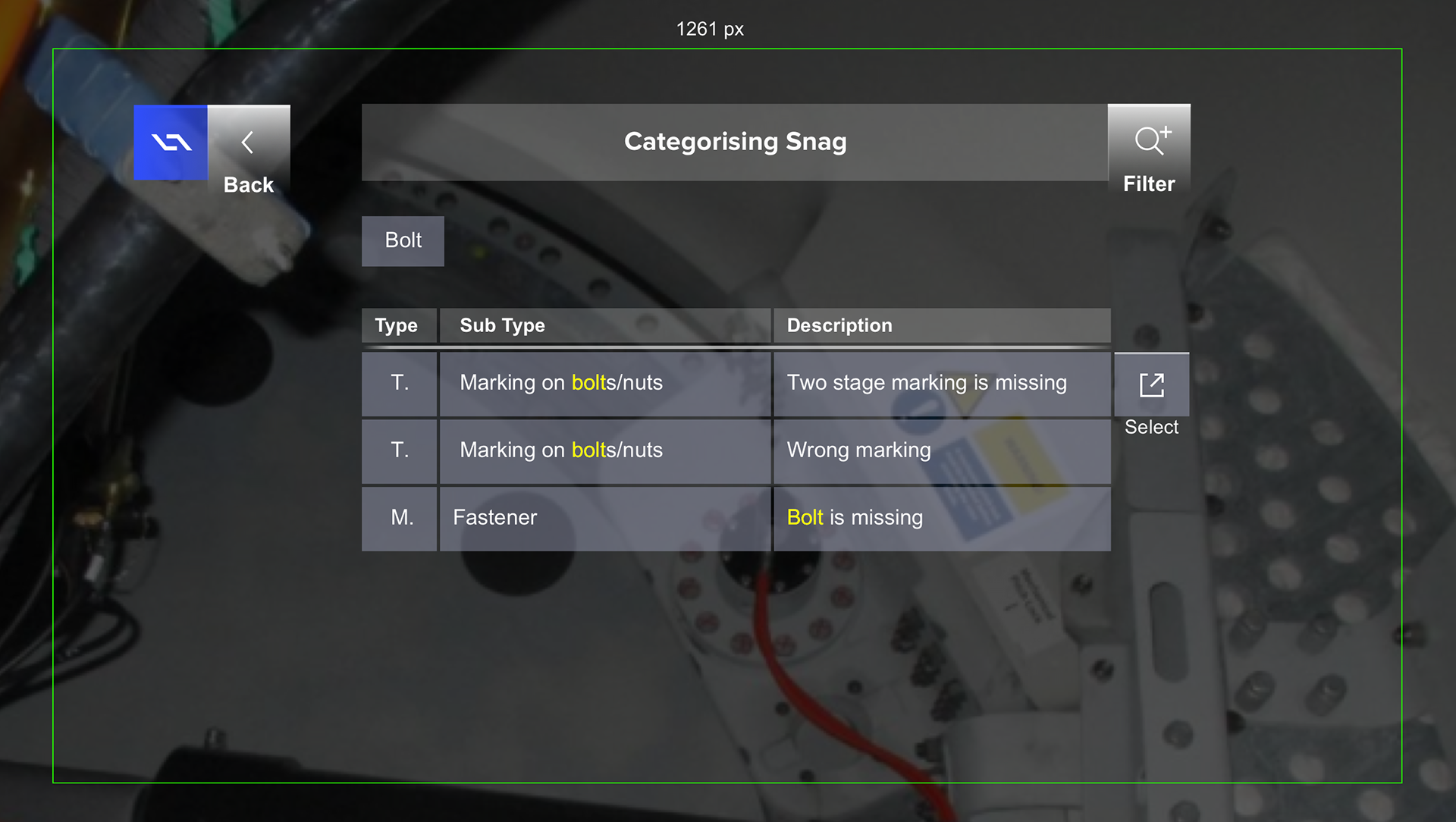
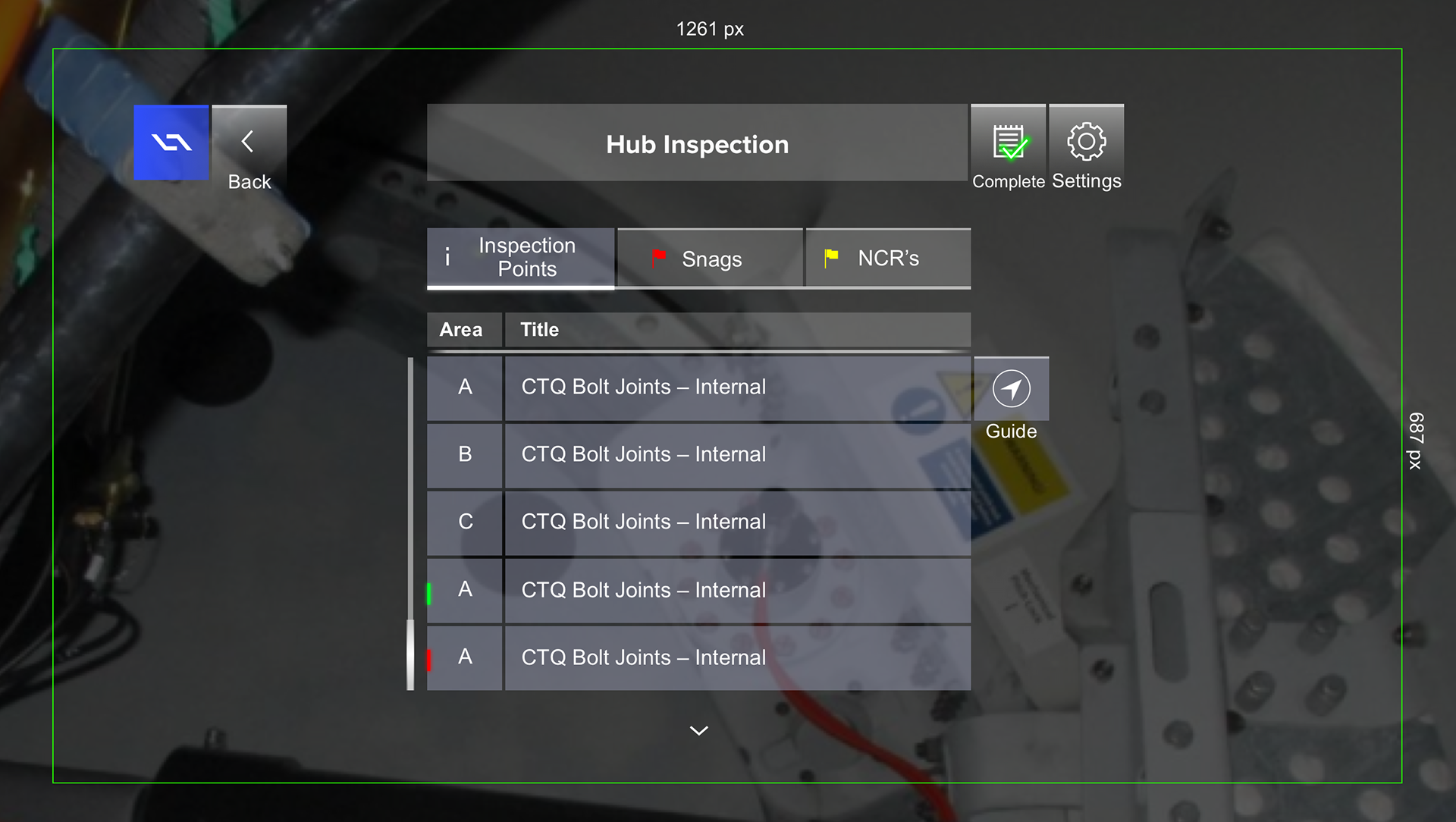
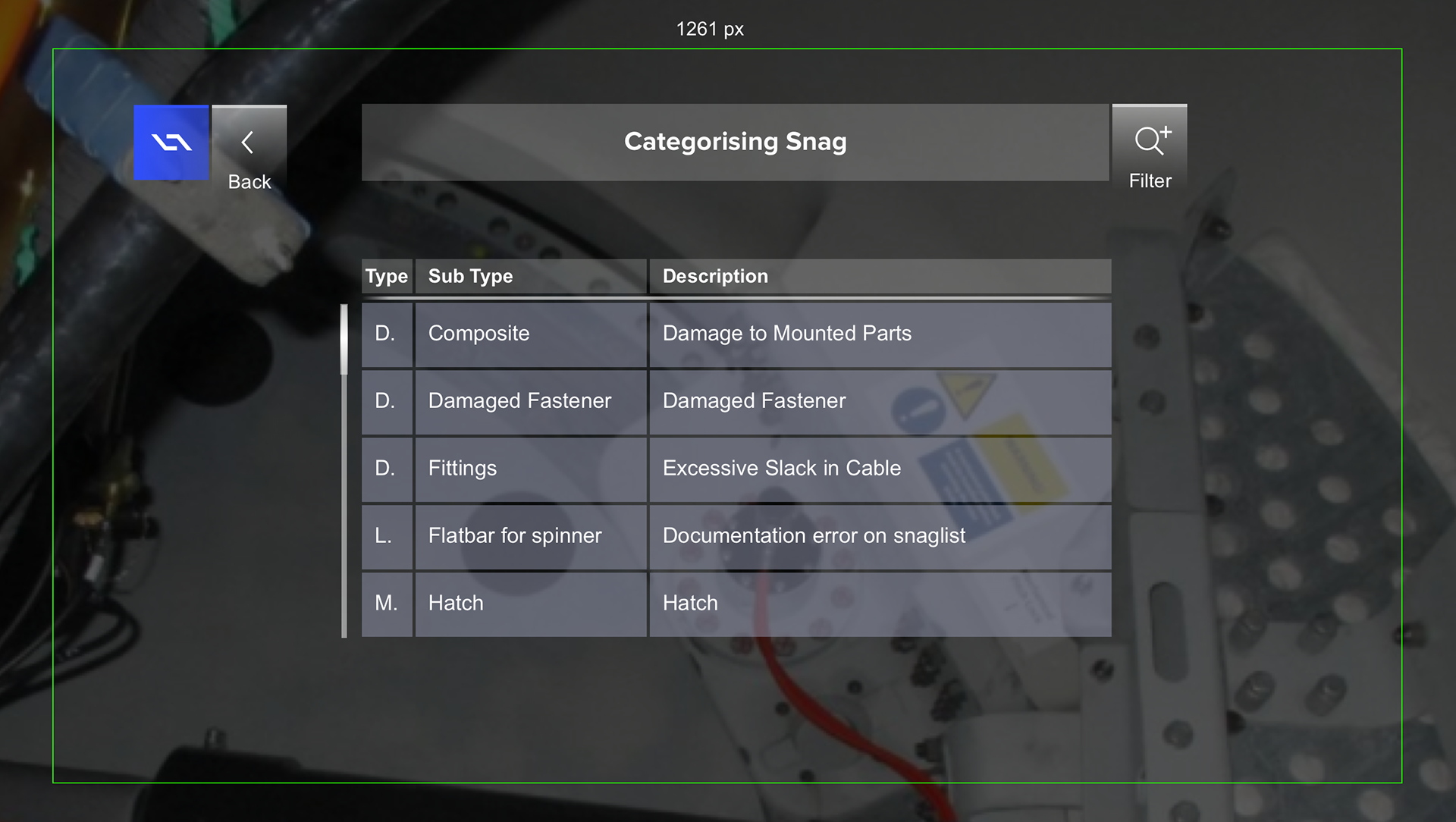
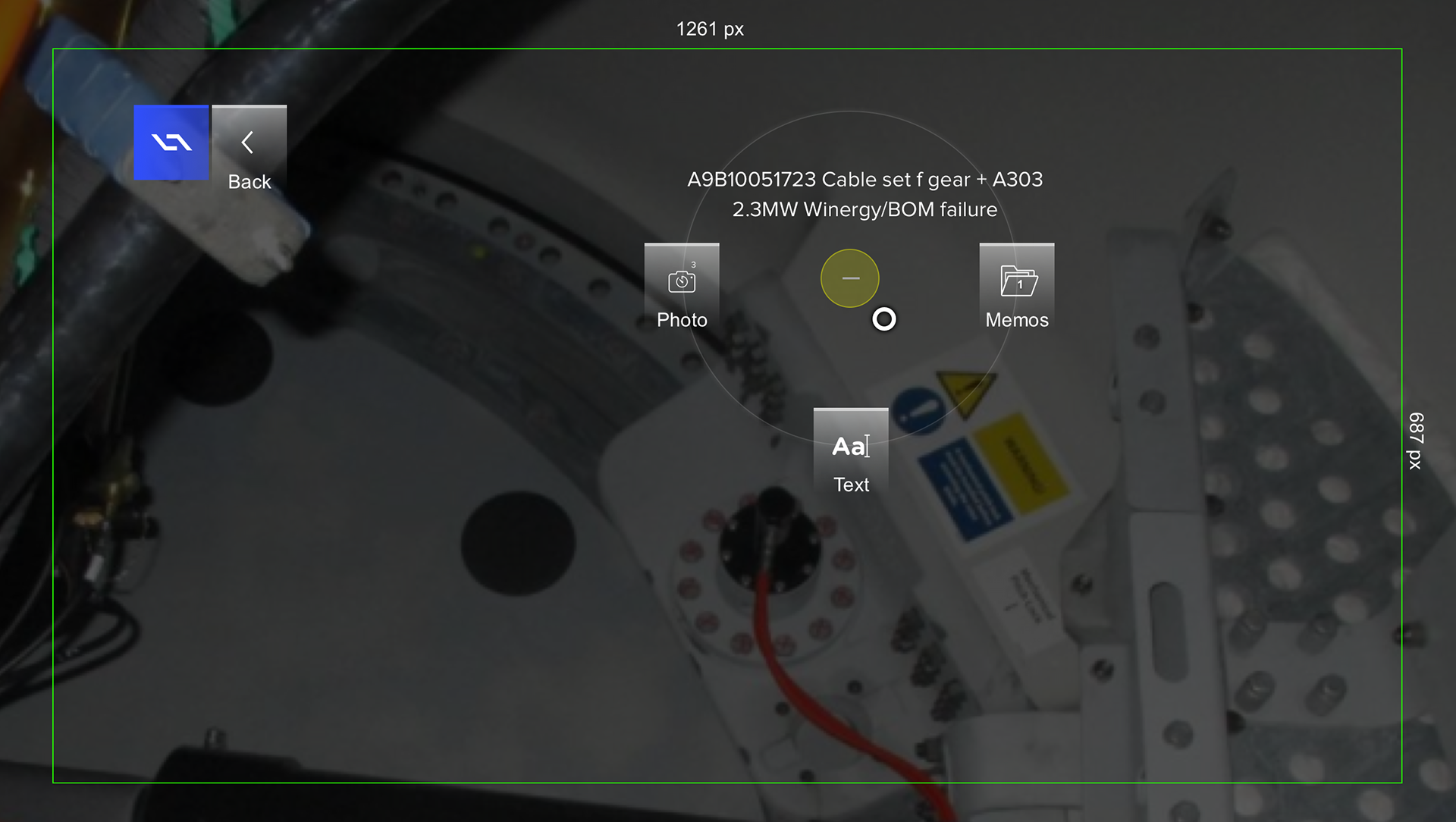
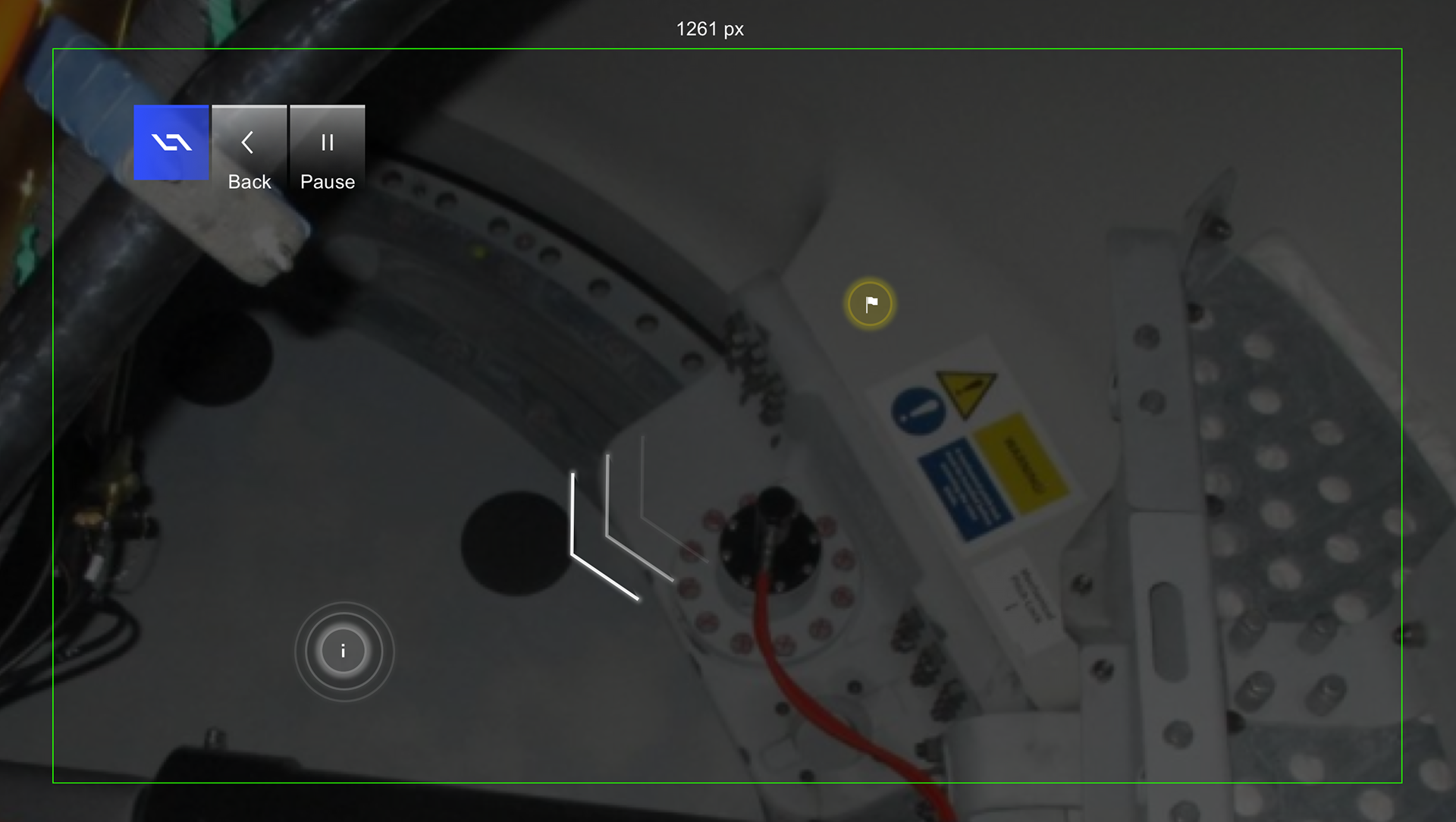
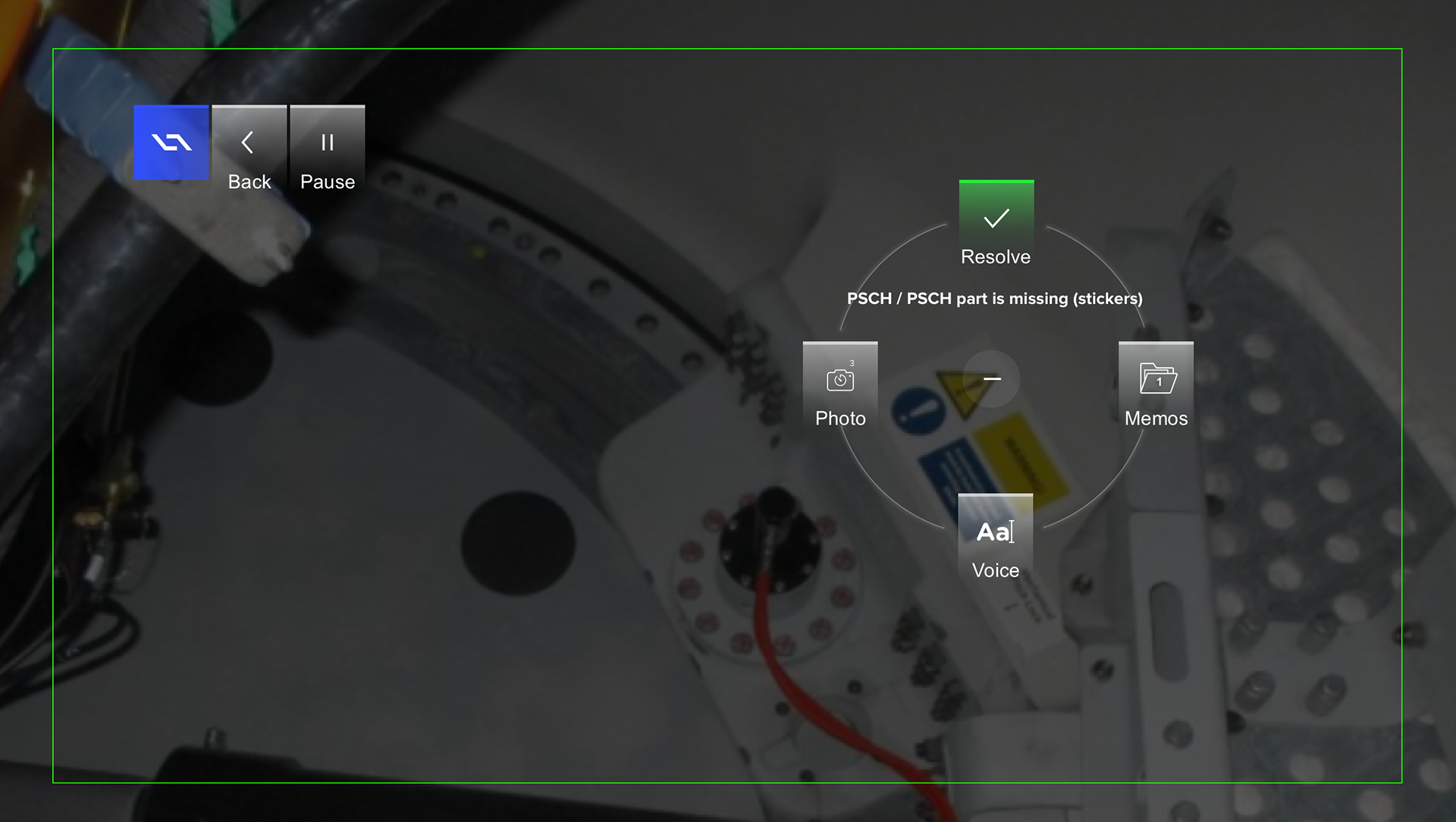
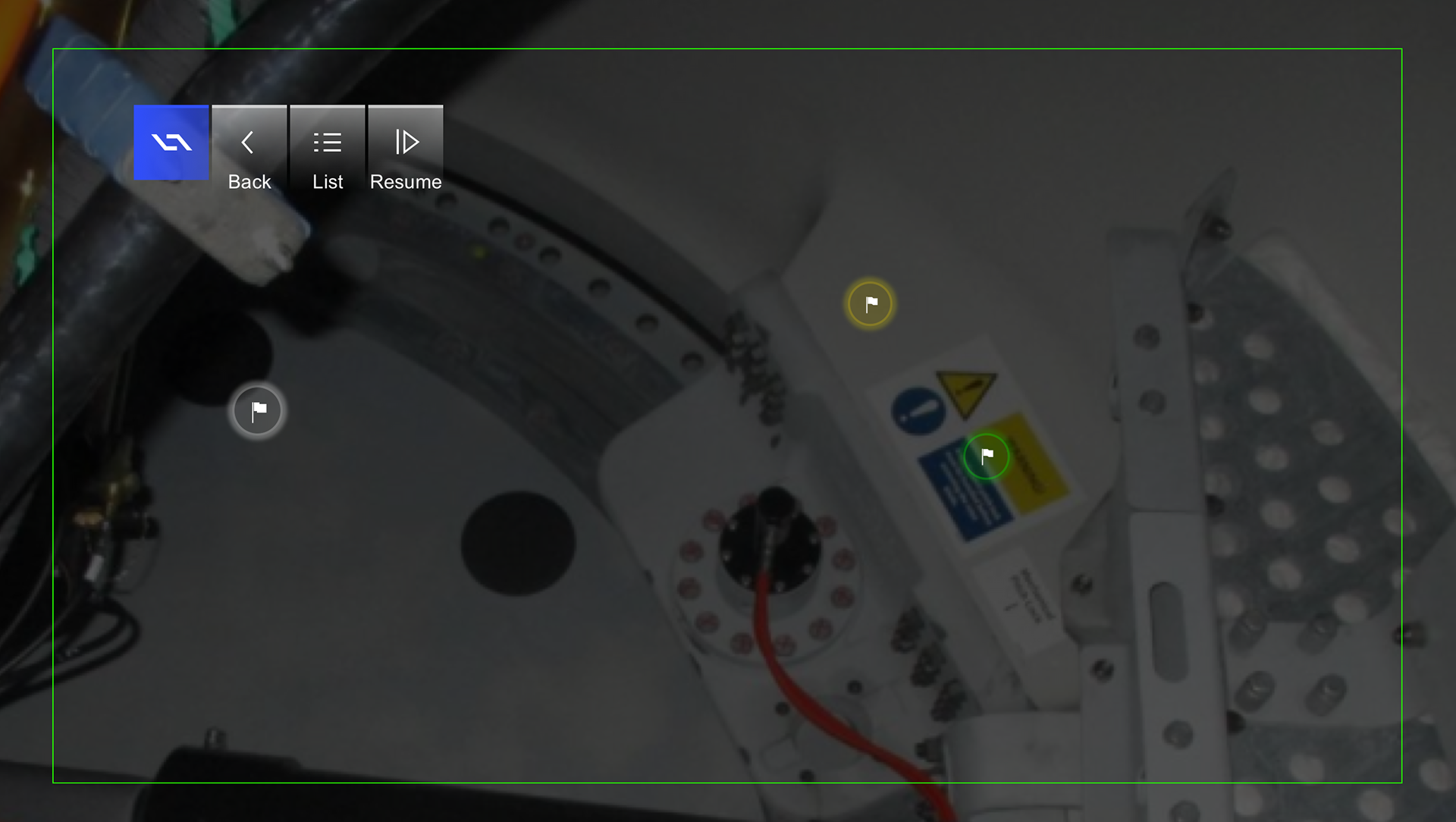
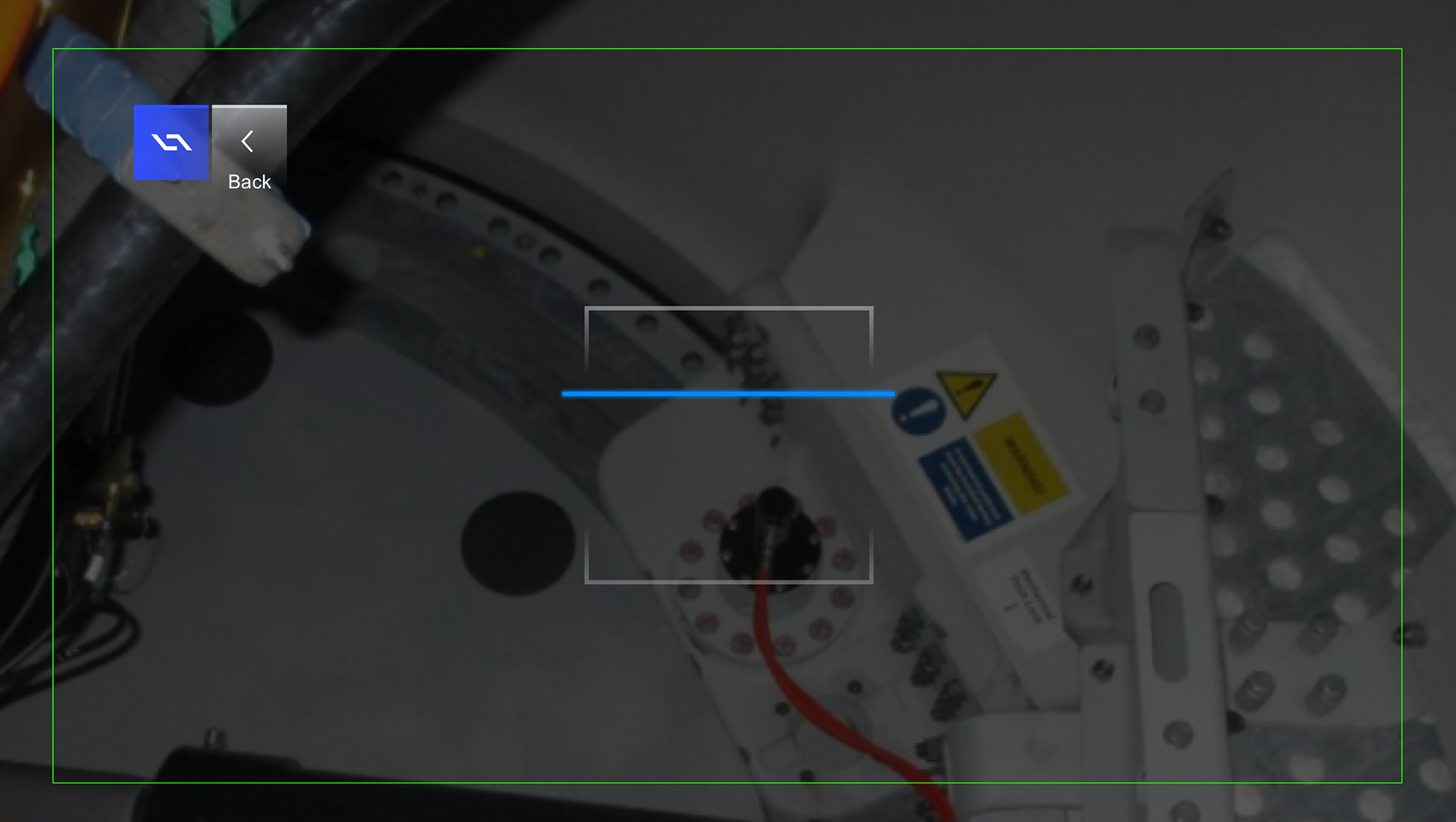
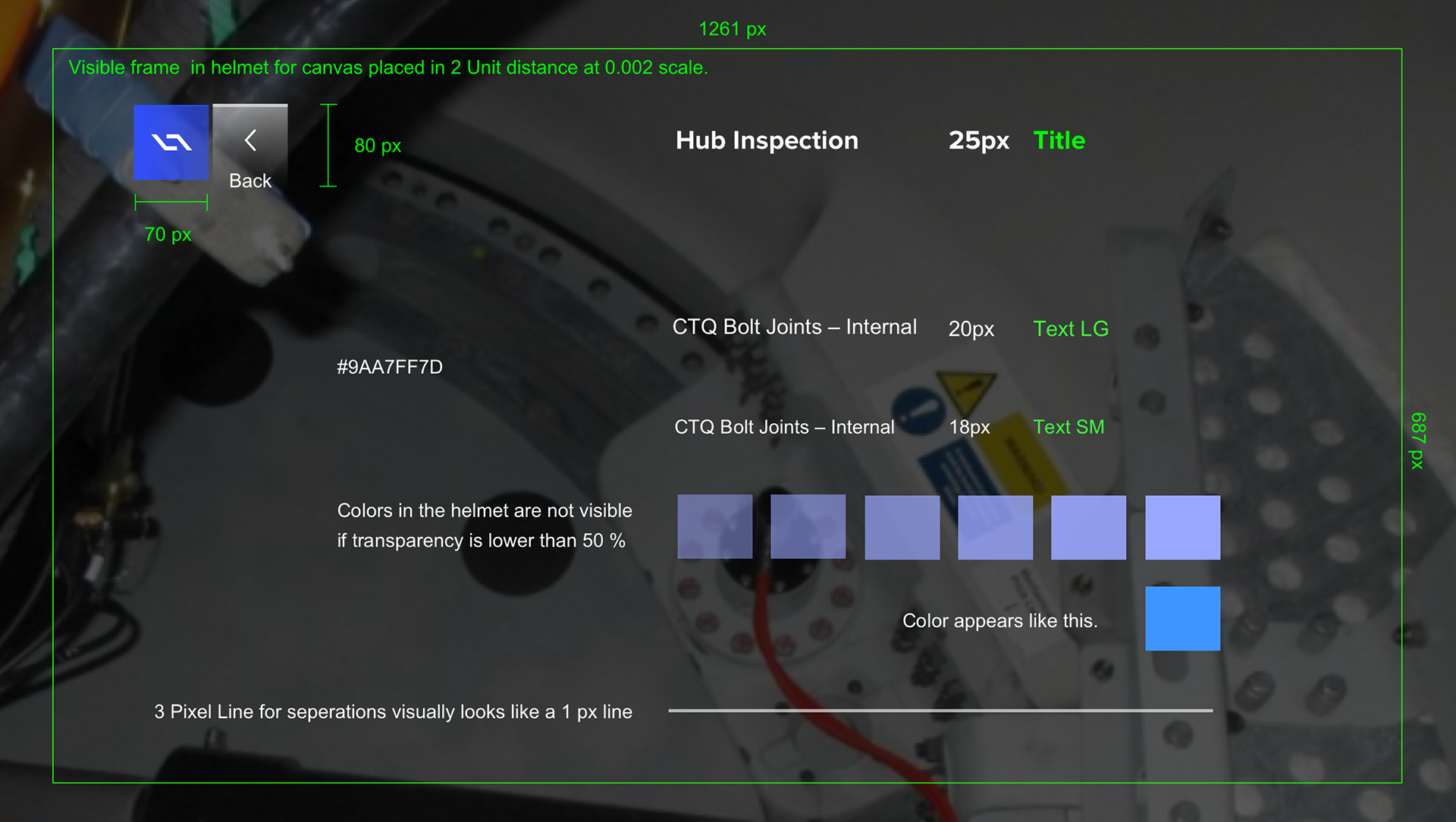
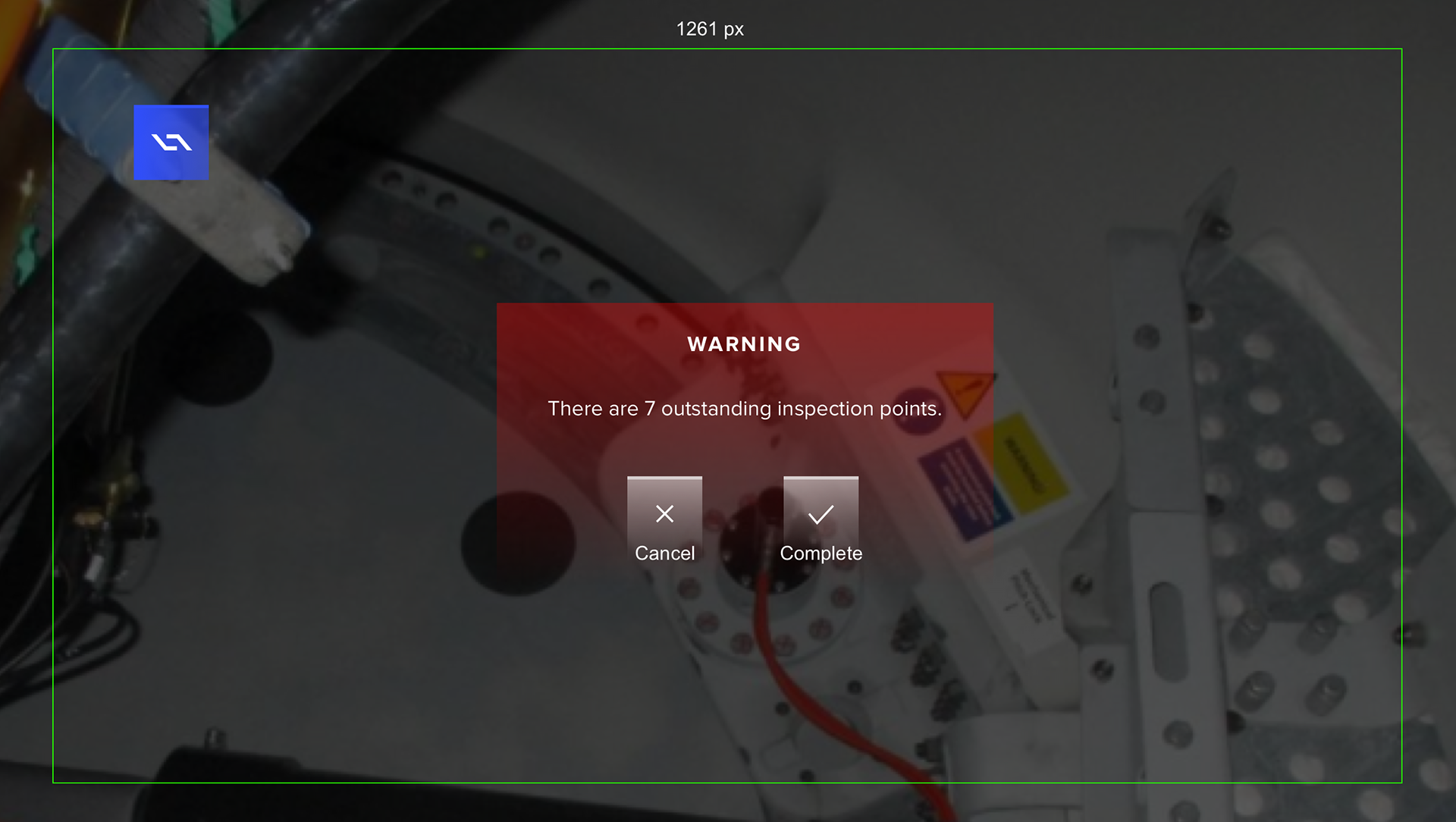
Share Design Revisions
To allow the Siemens team to continuously provide feedback, I shared a number of clickable prototype recordings with voice over explanations. The video was then shared with multiple stakeholder who reviewed the video and provided actionable feedback. This fast iterative process, to place several weeks before any code was written.
Tracking Feedback
To track the all feedback, from customers and internal internal user testing sessions, I created a Google Spread sheet template, that allowed us to document prioritise and assign the feedback.
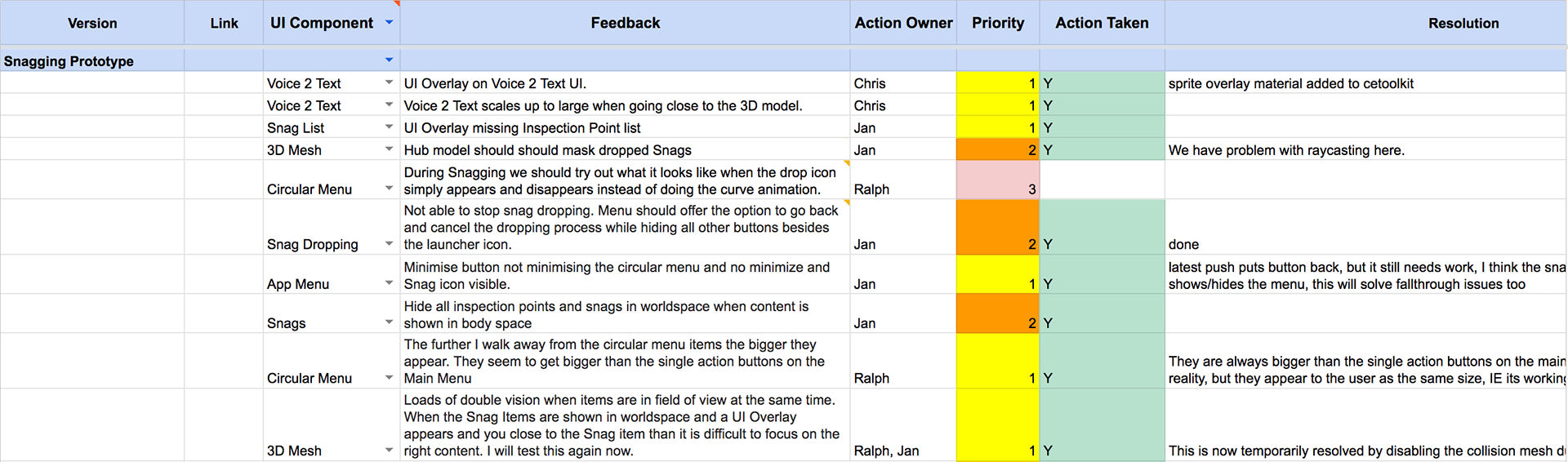
Onsite Training
With the help of the following button legend and an on-boarding video, we trained the inspectors on the Hub Inspection App.
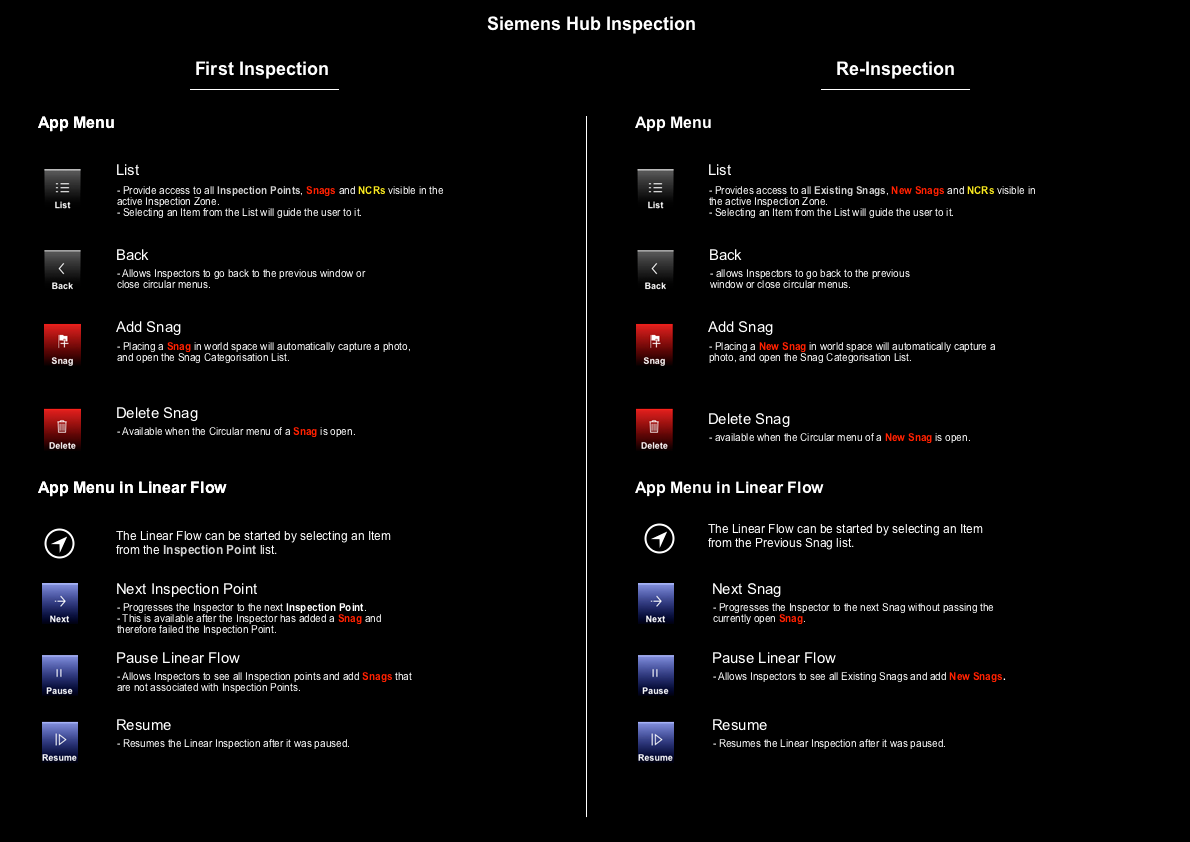
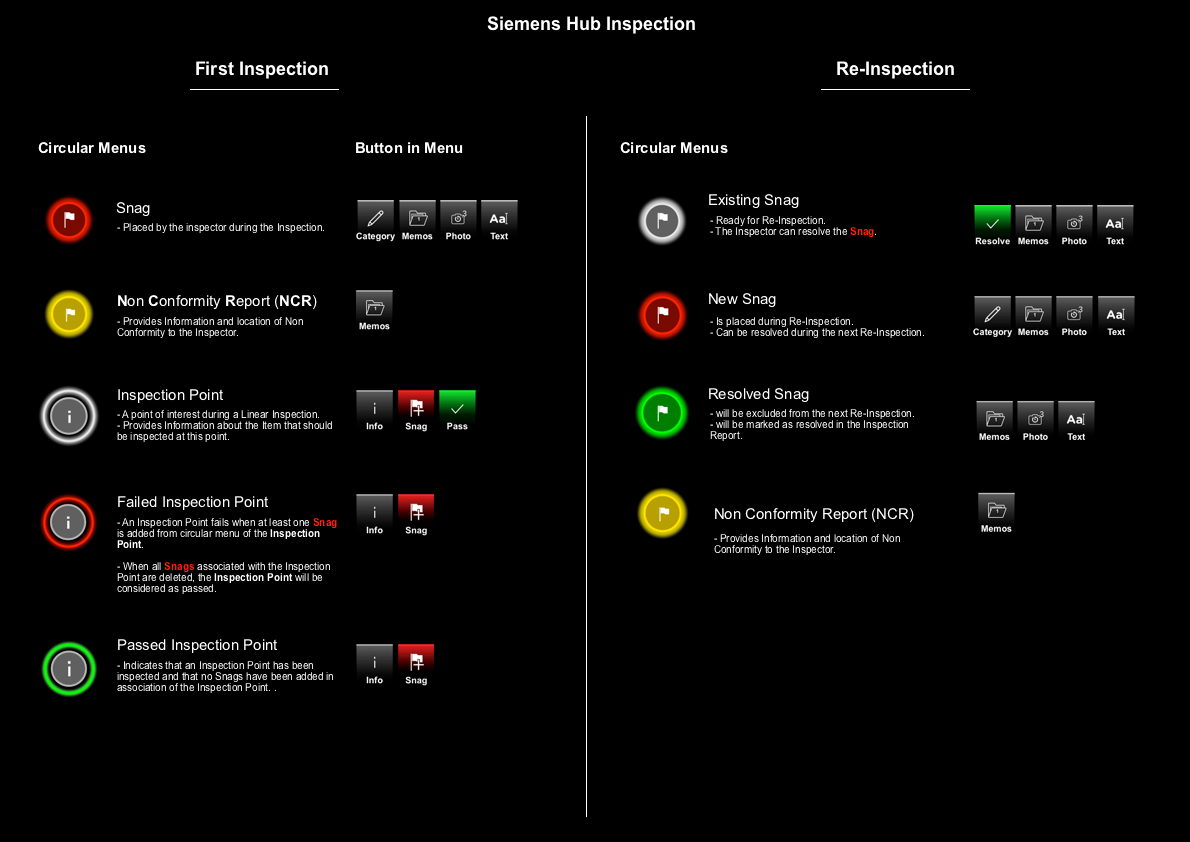
POV of Final Application
To demonstrate some of the key features of the AR Hub Inspection App, I have captured this POV which includes a virtual wind turbine hub to demonstrate what the experience in the Wind Turbine HUB is like.
• Viewing NCR's (Non Conformity Reports) The ability to present these where very valuable to the inspectors as it avoided them from re-snagging known deviations.
• Entering the linear inspection flow
• Creating Snaggs and placing them
Inspection Web Report
I created a simple HTML template that was populated with Snag and Inspection point data during the inspection. The image below shows an excerpt from the inspection report highlighting the location of the Snags placed within the hub, as well as the corresponding photo captured with the smart helmet.
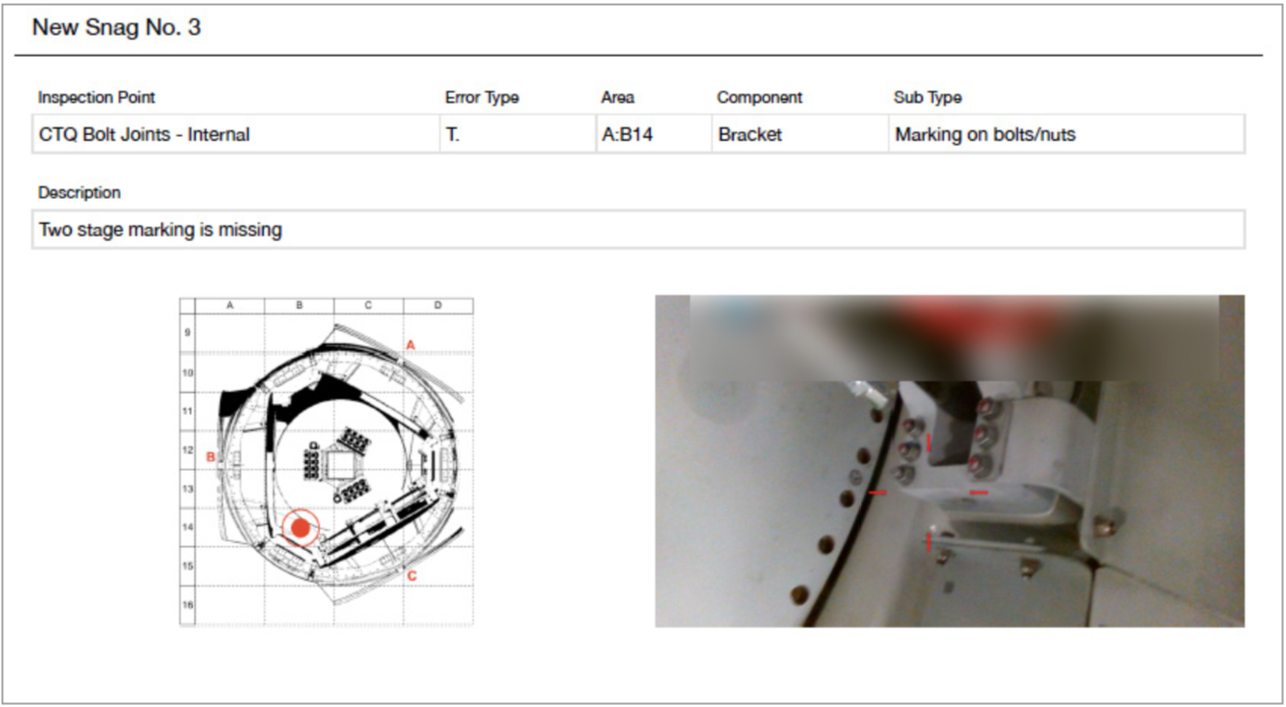
Onsite Validation
During the deployment of the hub inspection application, we conducted a study to examine the benefits of using AR for completing hub inspections. Key performance indicators (KPIs) included: time to complete an inspection with and without AR, number of errors with and without AR, questionnaire data after completing the DAQRI AR App (perceived usefulness, ease of use, usability, learnability, social influence/acceptance), and qualitative data. All KPIs were collected for two quality inspectors. The questionnaire and qualitative data were collected from six Novices (i.e., those who have never before completed a hub inspection).
The overall inspection was completed 44% faster with the DAQRI AR App, as compared to current methods.
Positive qualitative findings where:
• “Less documentation afterwards”
• “Guidance quality reassurance”
• “Repeatability and less administration”(sic)
• “Don’t forget an inspection point ,easy data collecting, easy handover to a colleague, opportunity to do the inspection during assembly”
The full Siemens - Gamesa case study can be found here.
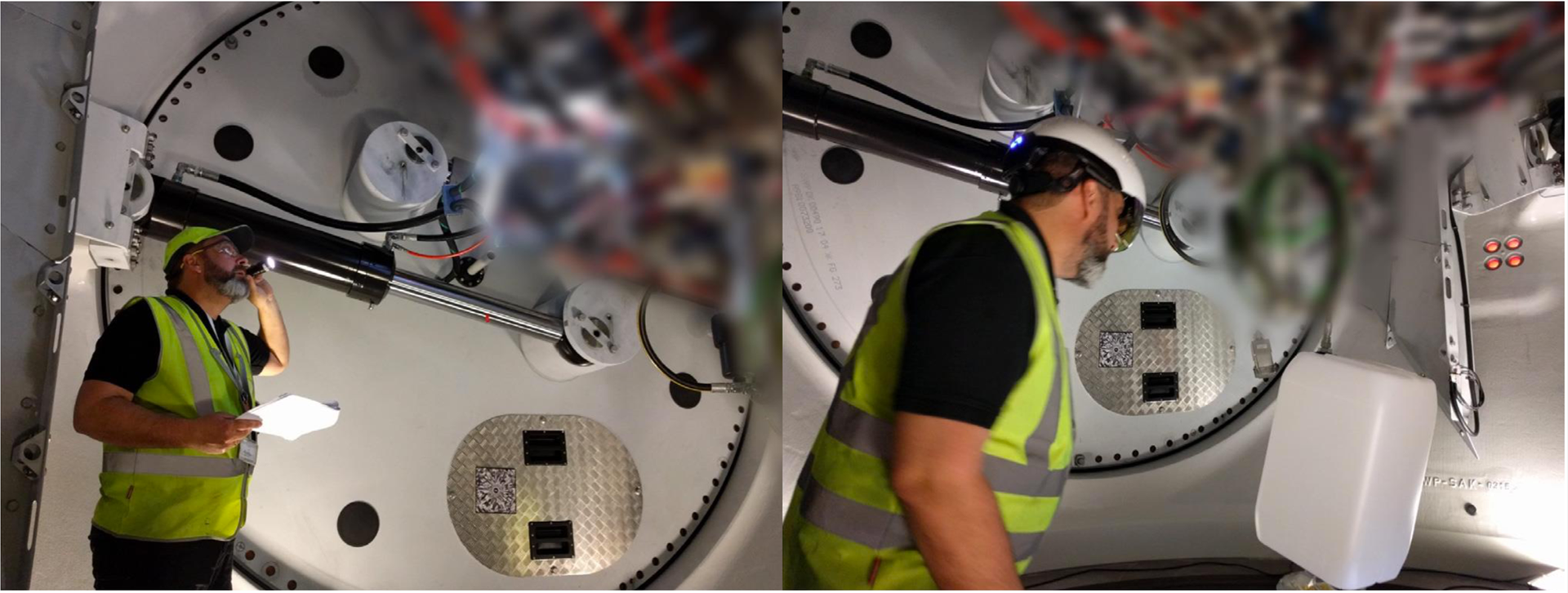
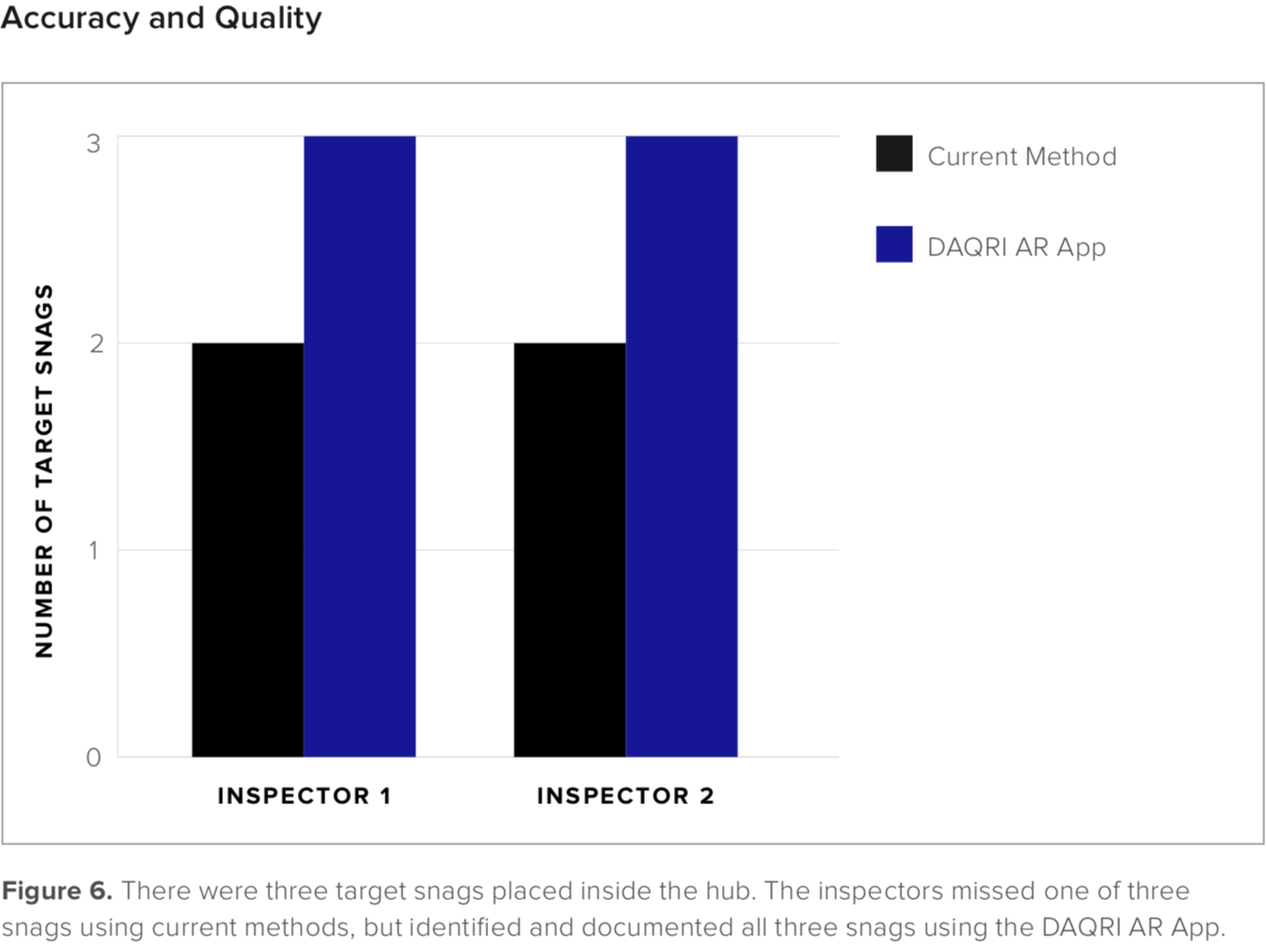
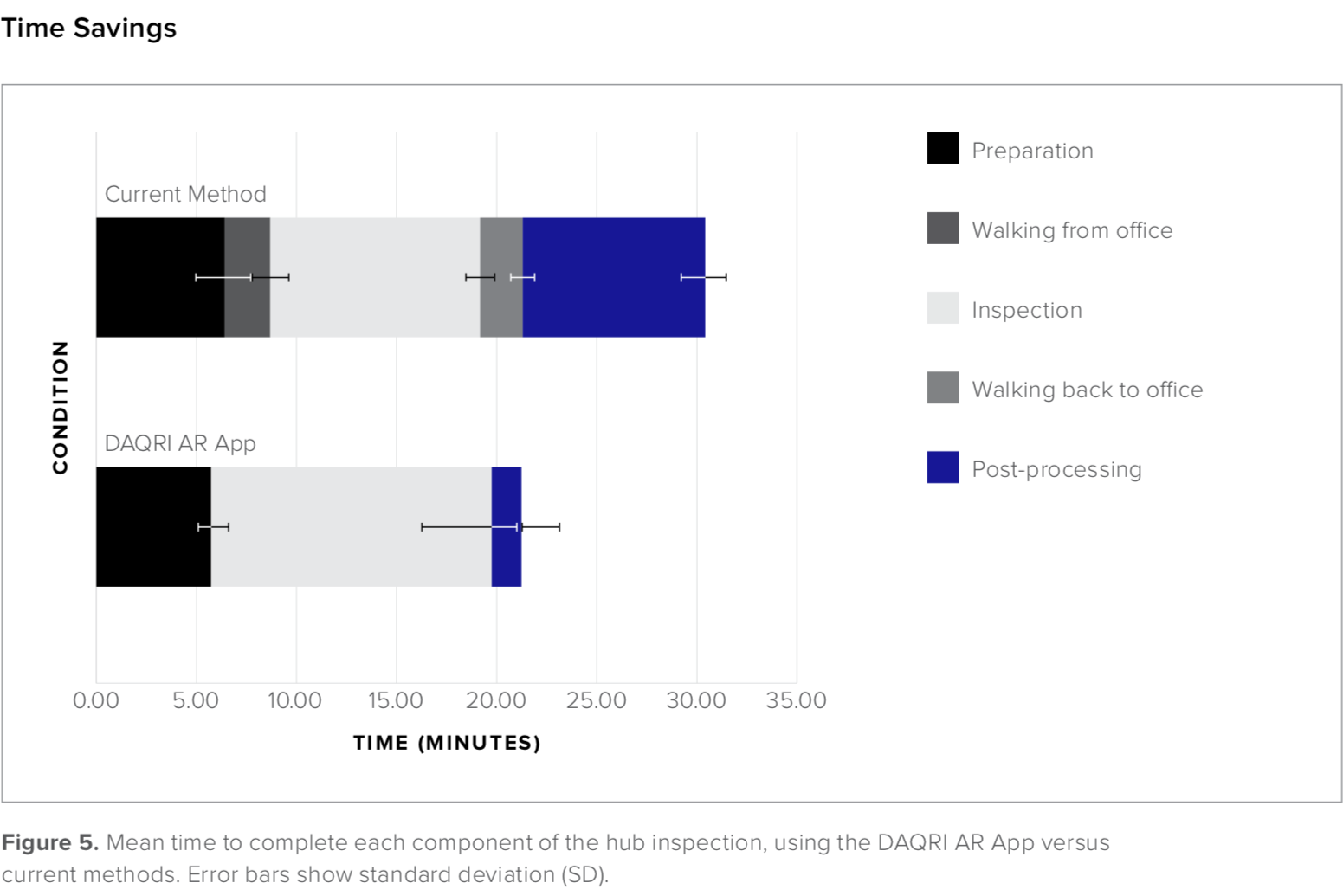